KUKA|prc for Dynamo Tutorials
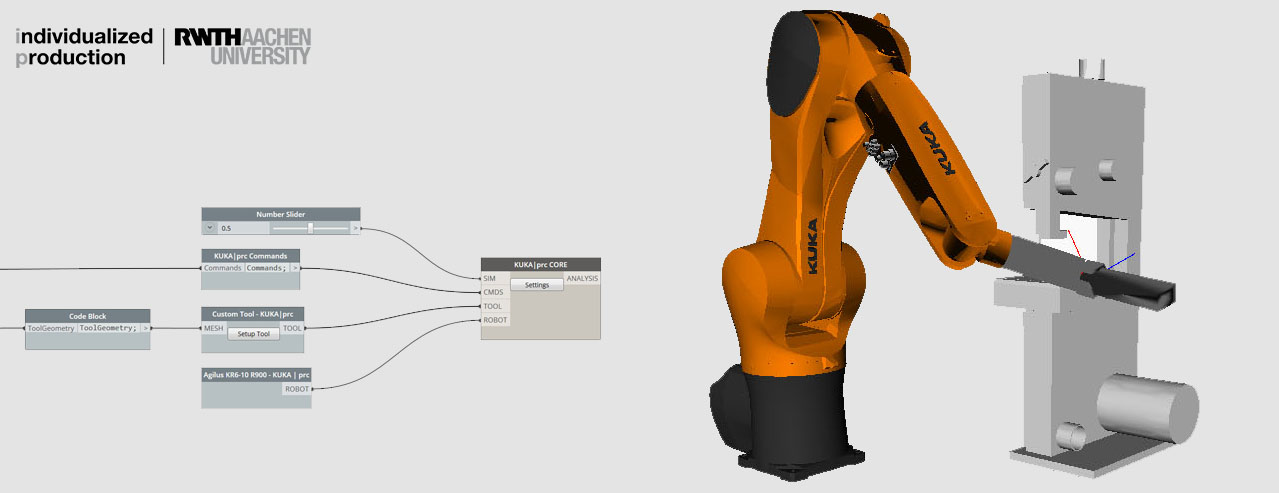
Welcome to our KUKA|prc for Dynamo tutorials on visual programming for robotic production.
The following information is intended for architects, designers, manufacturers, students and every individual who aspire to learn the basics of robotics, the challenges in using the robots and guidelines for robotic programming.
The latest beta-testing of KUKA|prc for Dynamo as well as the KUKA KMR iiwa were presented during the workshops at RobArch2018 and can be also seen in the RobArch2018 video of the workshop highlights.
KUKA|prc for Dynamo is a collaboration between IP RWTH Aachen University, the Association for Robots in Architecture and Autodesk. KUKA|prc for Dynamo Download (please scroll to the bottom of the page).
Basic Robotics
This section teaches the basics about industrial robots. Some learning objectives are the consideration of the physical constraints of a robot during the process development or the programming of robots using KUKA|prc in different visual programming environments. The order of physical robotics and robot programming is linked to each other so real world and digital representation can be connected. For the inexperienced user a comprehensive guide to visual programming from Autodesk Dynamo Studio is available. The following publication is also recommended for the interested reader: Towards cloud informed robotics
Downloads & Links:
Robodonien – robotic fabrication of timber frame structures
„Robodonien – robotic fabrication of timber frame structures“ shows an example for developing a robotic process with the help of Dynamo and KUKA|prc. It introduces a novel concept which uses a continuous production feedback and the integration of fabrication constraints. This methodology is demonstrated by the fabrication process of complex space frame timber structures using of a robotic setup and a bandsaw cutting process. The potentials and limitations of each fabrication resource are analyzed through design and construction of a 1:1 scale prototype developed at the Robodonien 2017 festival, Germany. The outcome of the research results in the creation of an intelligent computational program, which provides visual guidance for the user during the design process.
The video describes the process development while the PDF tutorials explain the requirements in programming.
Downloads:
Clay Printing - 3D printing of complex and freeform elements
This project demonstrates 3d printing of complex and freeform elements which are controlled by parameters in a computational design environment. The process was demonstrated at the AEC Hackathon 2018 Workshop, Berlin within the workshop “Robots in Architecture - Robot Process Hacking” which took place at the ISARC conference. Participants from around the globe learned how to program robots within the newly developed environment in a three day workshop. The workshop was structured in 3d printing toolpath development for variable geometries, understanding material and machine constraints and finally how to program a robot.
A further workshop was conducted at AEC Hackathon 2017 in Munich. It was focused on additive and subtractive manufacturing which can be translated for large scale construction. Impressions of the workshop can be found here.
Downloads:
These tutorials are only a foretaste on more e-learning material.
Friendly supported by